Поехали!.. Комплекс сушки вернулся в строй
21-11-2022, 12:07
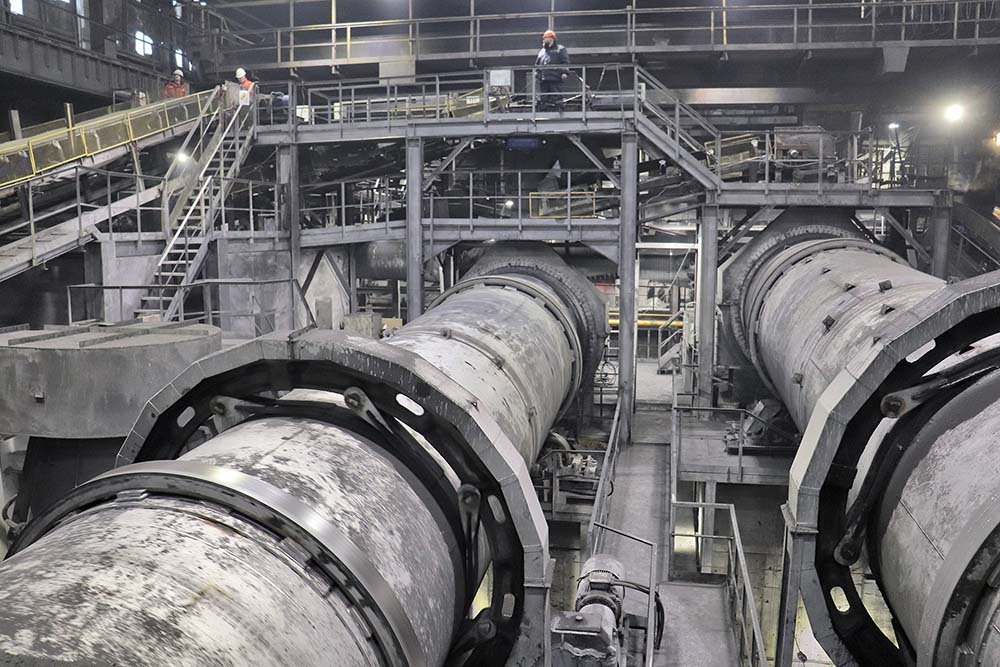
Часть мероприятий пришлось отложить до лучших времен по различным причинам. Одна из них – отсутствие поставок запчастей из-за невозможности их финансирования в текущих условиях. А те ремонты, которые все же удалось произвести, уже принесли первые плоды. Корреспондент «ВГ» отправился в ВОЦ, чтобы увидеть комплекс сушки в работе спустя три недели после его пуска в эксплуатацию.
По словам главного механика подразделения Алексея Дудина, в целом объект работает лучше, стабильнее, чем это было прошлой зимой. Однако доводить до ума его еще надо.
– Основную часть «узких мест» мы расшили, и это, безусловно, принесло свои плоды, – считает Алексей Витальевич. – Однако не все работает так идеально, как мы представляли. К примеру, система пневмообрушения, идею установки которой мы позаимствовали на ЕВРАЗ Качканарском ГОКе для решения проблемы налипания концентрата в бункерах. Система работает, хлопок получается хороший, но его силы не всегда бывает достаточно для обрушения всей массы концентрата в бункере над ленточным дозировочным питателем. Бывает, что часть налипшего концентрата остается, и приходится, как и прежде, выскребать эти остатки вручную. Так что делаем вывод – толк от новой системы есть, но она могла бы работать и более эффективно.
– После запуска комплекса мы столкнулись с еще одной проблемой, – продолжает главный механик цеха. – Она касается неравномерной подачи концентрата в барабаны, что сказывается на неравномерности его просушки. Проблема кроется в том же бункере, о котором мы говорили выше, и в установленном под ним дозировочном питателе № 373А. По идее, питатель должен работать в автоматическом режиме, четко дозируя количество концентрата, но нам лишь несколько дней назад удалось перевести его в этот режим. Дело в том, что дозировочный питатель дозирует нагрузку в заданных параметрах, ориентируясь на показания встроенных весов. Дозировка происходит автоматически за счет изменения скорости движения ленты, при этом бункер должен все время находиться под нагрузкой. Однако во избежание зависания приходилось переводить питатель в ручной режим с постоянной заданной скоростью, что не обеспечивало равномерность подачи концентрата в сушильные барабаны. Решением проблемы могла бы стать своя компрессорная станция (сейчас сжатый воздух мы получаем с шахты «Магнетитовая»), способная нагнетать более высокое давление в ресиверы системы пневмообрушения, но из-за ограниченного бюджета приобрести ее не удалось. В настоящее время мы рассматриваем возможность применения компрессора, законсервированного отделения флотации.
Кроме того, по словам Алексея Витальевича, в первую неделю после запуска комплекса сушки в цех пришла заказанная система байпасов. Система смонтирована и опробована. Как вы помните, мы говорили в прошлом месяце о том, что ее необходимо было установить на трубопроводы для снижения разрежения в сушильных барабанах, чтобы избежать затягивания в трубопроводы концентрата.
Еще одно нововведение, появившееся за летний период и показавшее свою эффективность, – это полиуретановые чистители, которые были установлены на перегрузочных узлах. Благодаря этим приспособлениям удалось значительно снизить налипание концентрата на транспортерные ленты и сократить количество просыпи.
Неплохо показали себя в работе новые анкерные крепления, а также хорошие результаты дала балансировка роторов на дымососах № 1 и 2. Таковы, по словам Алексея Дудина, итоги первых трех недель, прошедших после запуска комплекса сушки концентрата.
Алексей Витальевич провел меня по основным объектам комплекса сушки. Первое, что бросается в глаза, – воздух стал чище, цех – светлее, уровень шума – ниже. Однако, по мнению тех, кто занимается обслуживанием комплекса, улучшений требуют еще многие участки.
– Одна из самых больших проблем – высокая влажность исходного концентрата, – считает машинист сушильной установки Роман Косенков. – Показатели влаги в нем на выходе с участка мокрого обогащения могут варьироваться. Если идет сырой продукт, у нас забивает течки, приходится останавливать линию. Рабочие идут с кувалдами и очищают течку, на что требуется минут сорок. Но уже через двадцать – тридцать минут после повторного запуска линию можно вновь останавливать и снова браться за кувалду. Так проходит вся смена – довольно-таки бестолково и малопроизводительно в плане выпуска конечного продукта. На работу по очистке отвлекаются машинист сушильной установки и машинист конвейера.
– Физическая нагрузка – очень солидная, поэтому перчаток, которые выдают раз в месяц, мне не хватает, – включается в рассказ машинист конвейера Дмитрий Шубин. – Но все эти нюансы, как и многое другое, можно пережить, если учесть, что участок сегодня находится на стадии отладки. Со временем, надеюсь, все неудобства будут устранены, и мы будем работать уверенно и бесперебойно.
Комментариев 0